Injection molded plastic parts often require surface treatment for their final application purposes. Clients have multiple surface treatment options to choose from, and each technique has different effects on the texture, appearance, feel, and other surface characteristics of the parts. Surface treatment is a critical consideration for both clients and designers/engineers, as it significantly impacts the design of injection molds.
Why Surface Treatment is Necessary:
Most injection molds are made of aluminum and/or steel. Any imperfections on the mold surface, no matter how small, can be reflected in the final molded parts. If these imperfections are not removed through sandblasting or polishing, machining tool marks will remain on the finished product. In most cases, minor tooling marks inside parts that are not visible to the naked eye may not affect the appearance or functionality of the parts.
However, exposed surfaces often require additional processing. Nearly all molds undergo varying degrees of polishing. However, the finer the polishing, the higher the cost of the mold, and the longer the manufacturing lead time.

Injection mold without surface treatment
Key factors determining surface treatment:
Parts produced by injection molding and machining or 3D printing have different surface treatments. The surface finishing of the latter two is performed after the parts are made, and is a post-processing step; for the injection molding process, the mold itself needs to undergo such processing (or add texture), and the injection molded parts are the finished products. pieces. For example, if the finished part wants a matte surface, the inside of the mold must first be textured to give the injection molded part a matte effect. The key to determining surface treatment is the following two factors:
Improve part appearance:
The part’s designer may choose the texture of the finished product for different aesthetic reasons. Smooth or matte textures on the surface of parts can not only improve the appearance and give a sense of quality, but can also cover small defects such as flow lines, weaving lines, dents or shadow marks caused during the injection molding process. From a business perspective, parts with a better surface finish are more attractive to customers.
Improve part functionality:
Texturing the surface of parts can improve the adhesion of paint or stickers. For example, parts with matte texture are easier to paint, the paint lasts better, and matte texture is also better for labeling. Texturing also makes parts easier to hold. By surface treatment of the mold, we can also avoid over- or under-injection defects in plastic parts. A well-designed, textured part can also help expel air from the mold and avoid air entrapment.
Surface treatment process classification:
The two most common surface treatment classifications on the market are SPI and VDI, which we will discuss separately.

SPI:
The Society of the Plastics Industry (SPI) has developed a set of finishing process standards to represent the surface finish of finished parts. Molds can be polished or textured mechanically or by hand. Specific standards are shown in the table below:
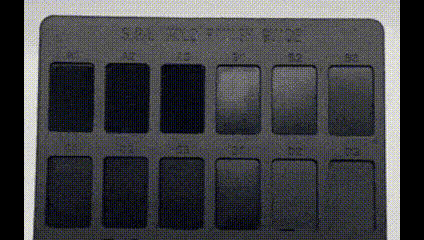
SPI Polishing level | illustrate | application | Surface roughness(Ra µm) | Applicable materials |
A-1 | 3# ,6000 Granular Diamond Paste | Mirror-like polishing requirements | 0.012- 0.025 | Acrylic |
A-2 | 6# ,3000 Granular Diamond Paste | Mirror-like polishing requirements | 0.025-0.05 | Acrylic, PC |
A-3 | 12# ,1200 Granular Diamond Paste | High polishing requirements | 0.05-0.10 | ABS, Acrylic. PS, Nylon, PC |
B-1 | 600 # sandpaper | Medium polishing requirements | 0.05-0.10 | ABS, Acrylic, PP. PS, HDPE, Nylon, PC |
B-2 | 400 # sandpaper | Medium polishing requirements | 0.10- 0.15 | ABS, Acrylic, PP. PS, HDPE, Nylon, PC |
B-3 | 320 # sandpaper | Low to medium polishing requirements | 0.28-0.32 | ABS, Acrylic, PP. PS, HDPE, Nylon |
C-1 | 600 Whetstone | Low polishing requirements | 0.35-0.40 | ABS, Acrylic, PP. PS, HDPE, Nylon, TPU |
C-2 | 400 Whetstone | Low polishing requirements | 0.45-0.55 | ABS, Acrylic, PP. PS, HDPE, Nylon, TPU |
C-3 | 320 Whetstone | Low polishing requirements | 0.63-0.70 | ABS, Acrylic, PP. PS, HDPE, Nylon, TPU |
D-1 | Sand blasting (coarse glass beads) | matte surface | 0.80-1.00 | ABS, PP. PS, HDPE, Nylon, PC, TPU |
D-2 | #240 Oxide Sandblasting | Matt surface | 1.00-2.80 | ABS, PP. PS, HDPE, Nylon, TPU |
D-3 | #24 Oxide Sandblasting | Matt surface | 3.20-18 | ABS, PP. PS, HDPE, Nylon, TPU |
VDI (STD)
The VDI 3400 surface roughness standard (often referred to simply as the VDI standard) is another set of mold texture standards set by the German Engineering Association (VDI). The VDI 3400 surface treatment standard mainly applies to parts using the electrical discharge machining (EDM) process. Some traditional surface treatment processes (like SPI) are also applicable to the VDI standard. Although this set of standards was developed by the German Engineering Association, VDI standards are widely adopted by manufacturers in many regions around the world, such as North America, Europe and Asia.

The VDI standard uses different parameters to represent the surface finish of components. From the animation above, you can see the surface treatment effects corresponding to different VDI parameters.
VDI parameter | illustrate | application | Surface roughness (Ra µm) |
12 | 600 Whetstone | Low polishing requirements | 0.40 |
15 | 400 Whetstone | Low polishing requirements | 0.56 |
18 | Sand blasting (coarse glass beads) | matte surface | 0.80 |
21 | #24 Oxide Sandblasting | Matt surface | 1.12 |
24 | #24 Oxide Sandblasting | Matt surface | 1.60 |
27 | #24 Oxide Sandblasting | Dull finish | 2.24 |
30 | #24 Oxide Sandblasting | Dull finish | 3.15 |
33 | #24 Oxide Sandblasting | Dull finish | 4.50 |
36 | #24 Oxide Sandblasting | Dull finish | 6.30 |
39 | #24 Oxide Sandblasting | Dull finish | 9.00 |
42 | #24 Oxide Sandblasting | Dull finish | 12.50 |
45 | #24 Oxide Sandblasting | Dull finish | 18.00 |