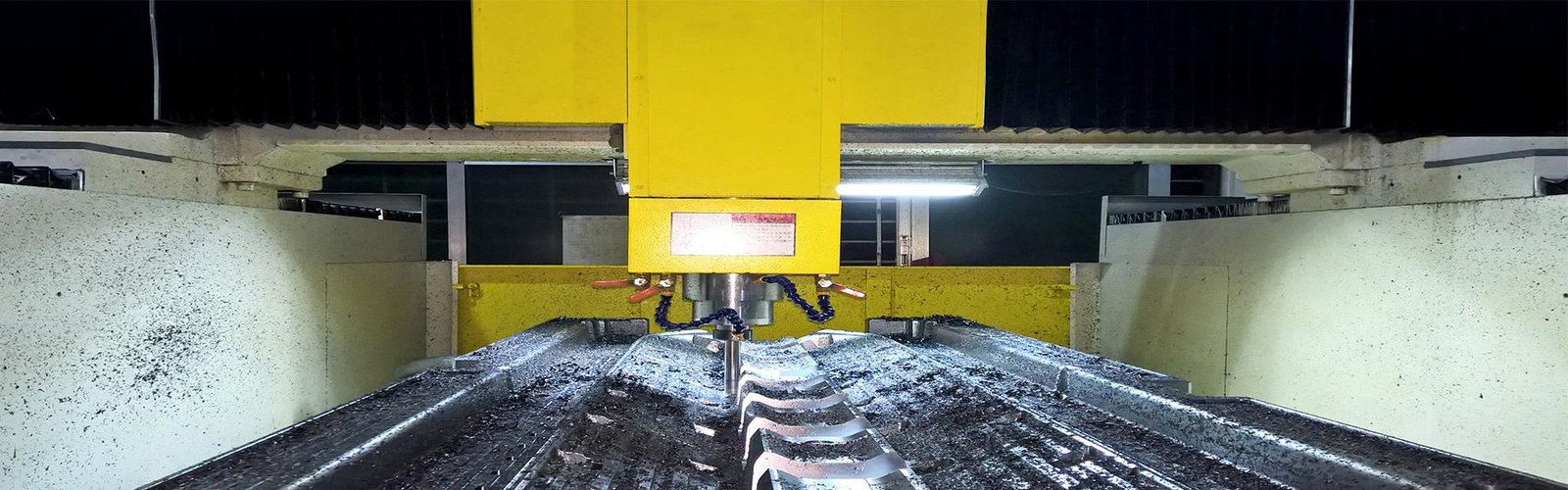
The Latest Advanced And Efficient Injection Stretch Blow Molding Machine
The injection stretch blow molding process is divided into four stages: injection, stretching, blow molding, and removal. After the plastic is melted, it is injected into a mold to form a preform, and then the preform is adjusted to an appropriate temperature to be stretched and blown to form a final shape. When the preform is in the mold, a stretching rod is inserted therein, the preform is stretched in the longitudinal direction, and the preform is blown in the circumferential direction by two-stage air pressure. After a certain period of cooling, the mold is opened, and the preform is taken out using a blanking chute or a robot, and the process is repeated.
With the development of the single-stage injection stretch blow molding machine Blowliner, Kiefel’s subsidiary Mold&Matic has opened up new markets. The machine is now used in the pharmaceutical and food industries.
The Blowliner is available in three sizes. The best-selling Blowliner Medium with a maximum material throughput of 130kg PET per hour can be used to process PET, PP and HDPE as well as smaller and larger models. Thanks to the intelligent concept of the machine, it can be upgraded at any time for the production of multi-layer products.
The entire stretch blow molding unit is equipped with a servo motor drive for extremely high reproducibility, precision and energy efficiency. The pre-blowing pressure and main blow pressure can be set in 0.1 bar increments using valve technology. During the verification process, the blow molding study according to the customer’s requirements determines the proper material distribution in the blow mold.
Another solution is that the process monitoring system can use a pressure sensor to measure the main blow pressure during operation of the main blow valve. If the pressure drops suddenly, the plastics manufacturer will immediately receive an alarm message. If requested by the customer, Blowliner can be used as a spray blow molding machine without the need for tensile elements. At the end of the blow molding process, the vacuum gripper of the integrated linear take-up system takes the finished product out of the mold and places it precisely on the conveyor belt or directly in the box.
In the Blowliner design phase, the company considered many aspects of mold technology. The solution is a balanced hot runner mold with a needle locking system. The Blowliner M has a cycle time of 10 seconds and the small Blowliner S has a cycle time of less than 8 seconds, providing the market with an injection stretch blow molding technology that delivers superior product quality, flexibility and productivity.