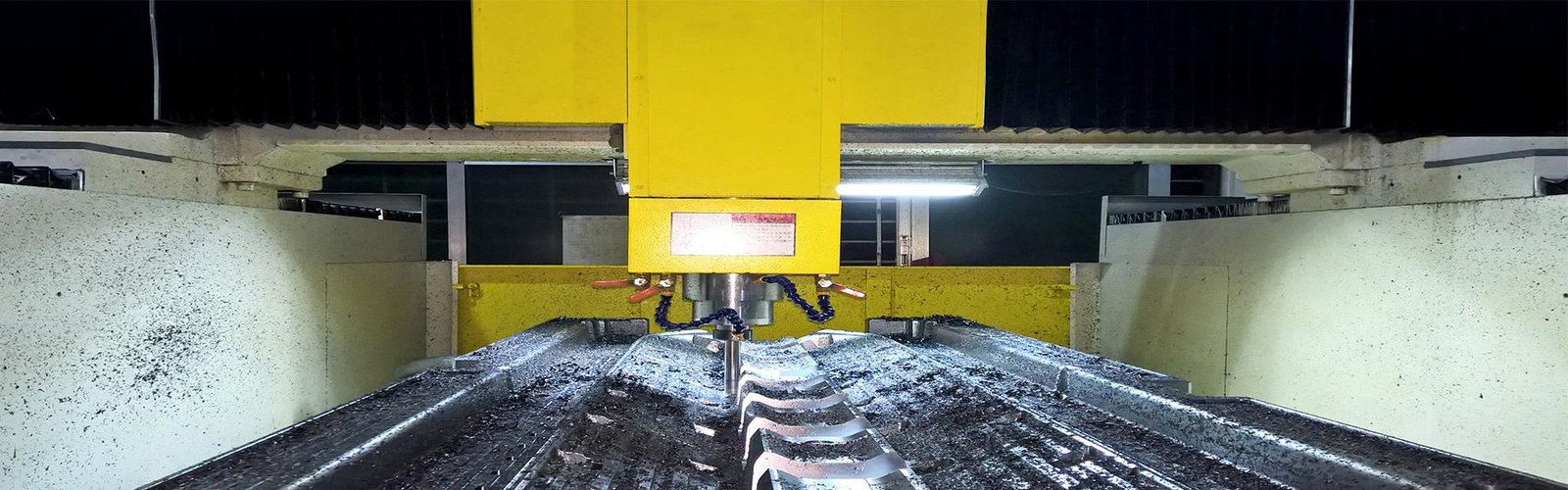
ENGEL Debut At 2018 Taipei International Plastics And Rubber Exhibition
Single source integrated manufacturing unit
Kurt Hell, Vice President, Medical Services, ENGEL, said: “The demand for high-end solutions for LSR processing is growing rapidly.” “By adapting the production line to individual products and quantities, we can ensure that our customers are highly competitive. If manufactured The components in the unit are adjusted from the start, and we can maximize the efficiency and quality potential.”
To integrate other peripherals and molds with robotics and process technology, ENGEL has established a global network of system partners. “In Asia, we have very strong partners, and like us, they are able to achieve the ideal solution because they are familiar with the needs of local manufacturers,” says Hell. “By working with local suppliers, we ensure cost-effectiveness for high-demand applications while maintaining a short delivery time for the entire system.” The Asian system partners who participated in the show were Taiwanese moldmaker HR Silicone and established in Guangzhou, China. 2KM of the Asian Division.
Self-optimizing injection molding machine
In addition, Industry 4.0 is another growing trend in Asia that will attract visitors to the ENGEL booth at the TaipeiPlass International Plastics and Rubber Industry Show. “Industry 4.0 is a major driver of efficiency and quality,” Kurt Hell emphasizes. “We help our customers embark on the road to smart factories by developing tailor-made products.” The modular approach of the ENGEL inject 4.0 solution allows manufacturers to easily take advantage of the opportunities offered by Industry 4.0. Even small-scale, personalized solutions can deliver significant benefits. For example, ENGEL will showcase its iQ weight control assist system in Taipei. During the injection molding process, the software analyzes the pressure curve in real time and compares the measured values by reference period. For each injection, the injection profile, transition point, and maintenance pressure are automatically adjusted to current conditions, and the injected melt volume remains constant throughout the production run. In this way, fluctuations in environmental conditions and raw materials are automatically identified and readjusted before a single waste is produced.