Sheet metal part is used in a variety of industries namely car manufacturing, aircraft parts, tools, agriculture, mining, catering, shipping, medical, electronic parts, and construction to name a few.

Stamping dies are the tools that shape and cut sheet metal parts. They are commonly developed using computer-aided design (CAD) software and analytical programs to create and prove-out highly accurate, unambiguous designs. These designs are then translated into stamping dies by skilled craftsmen, known as diemakers. Once these stamping dies are mounted into presses, sheet metal is fed to them to produce parts.
Different from plastic injection molding or metal injection molding, metal stamping is a cold-forming operation, which means that no heat is introduced into the die or the sheet material intentionally.
There are many kinds of stamping dies, all of which perform two basic operations—cutting, forming, or both. Manually or robotically loaded dies are referred to as line dies. Progressive and transfer dies are fully automated.
The most common types of dies perform cutting and forming. Cutting dies are used to shear sheet material into what is called a blank. These blanks are then exposed to blanking dies which cut the entire perimeter of the part, or to forming dies where the blank is stamped into a part. Punching is another function of cutting dies. Punching is the cutting of a slug from the sheet metal stock to produce a hole or slot. Cutting dies are also used to trim excess metal from around a formed part.
Hole punching and other cutting operations require specific and carefully maintained clearances between the punch (male component) and the die (female component). The setting of the required clearances is determined by both the stock thickness and temper. In general, die clearances increase as the stock thickness increases. The depth of punch penetration into the sheet metal stock will also increase as softer stock is used.
Forming is a general term used to describe a stamped part whose shape and contour is reproduced directly from the shape and contour of a die set. The main forming operations accomplished with press mounted dies are:
• Drawing
• Bending
• Flanging
• Hemming
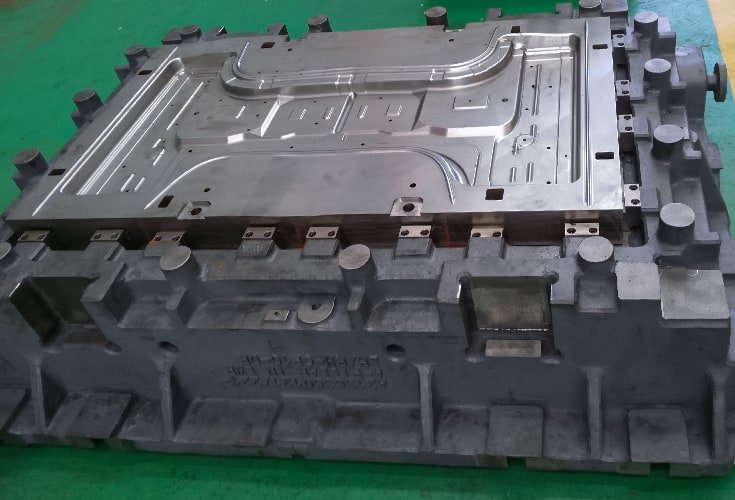
Drawing, or draw forming, involves forcing a blank deeply into a die cavity and shaping it into the shape and contour of the punch face and sides. Without sufficient formability qualities, drawn blanks are subject to wrinkling, thinning, and fracturing. Draw forming requires an addition to the die set called a “blankholder”. The function of the blankholder, usually a ring through which the punch and ram pass, is to control the metal flow as it is forced into the die cavity. In practice, the blankholder must exert less pressure against the blank than the punch, so metal can flow into the die; yet it must exert enough pressure to prevent the material from wrinkling.
Bending is a relatively simple forming operation which provides rigidity and shape to sheet metal parts. Like bending is flanging. However, a flange is significantly smaller in dimension than the rest of the part. The functions of a flange include:
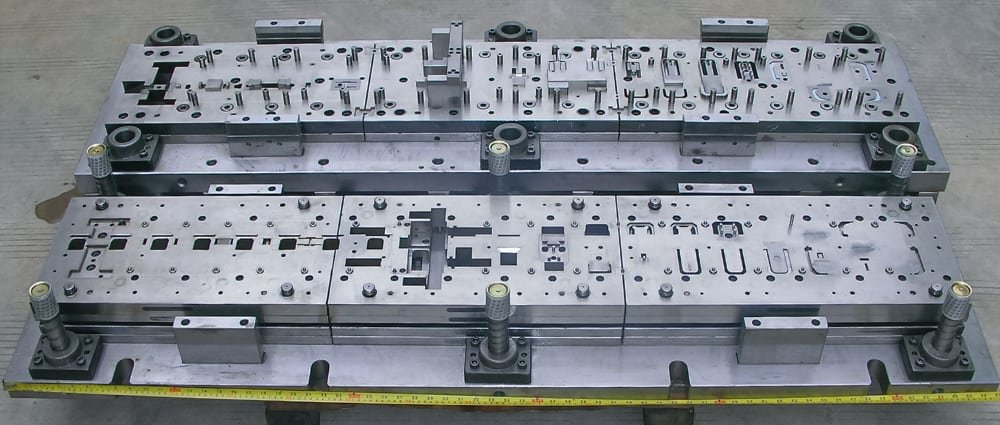

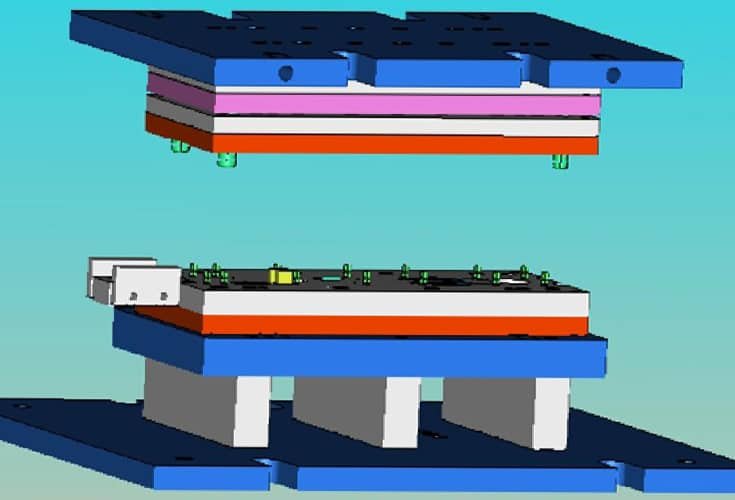
• giving a more finished appearance
• rigidity
• edge strengthening
• providing a fastening or attachment surface
Hemming is the folding over of a short flange upon itself to form a smooth, rounded edge and to facilitate the attachment of mating parts.
Multiple stamping operations may be performed within a single die, or at several die stations within a die set and with a single stroke of the press.
Single station dies can be either compound dies or combinations
dies. A compound die performs basic cutting operations such as blanking and hole punching to produce parts. Combination dies combine shaping and forming functions with cutting operation to manufacture parts.
Multiple station dies are arranged so that a series of sequential operations are accomplished with each press stroke. Two die types are used; progressive and transfer. With progressive dies, coil stock is fed into the press. Individual stampings are connected with a carrier strip as they progress through the various die operations and are ultimately separated and then discharged from the press. In transfer die operations individual stock blanks are mechanically moved from die station to die station within a single die set. Large stampings are done with tandem press lines where the stock is moved from press to press in which specific operations, such as drawing or trimming, are performed.
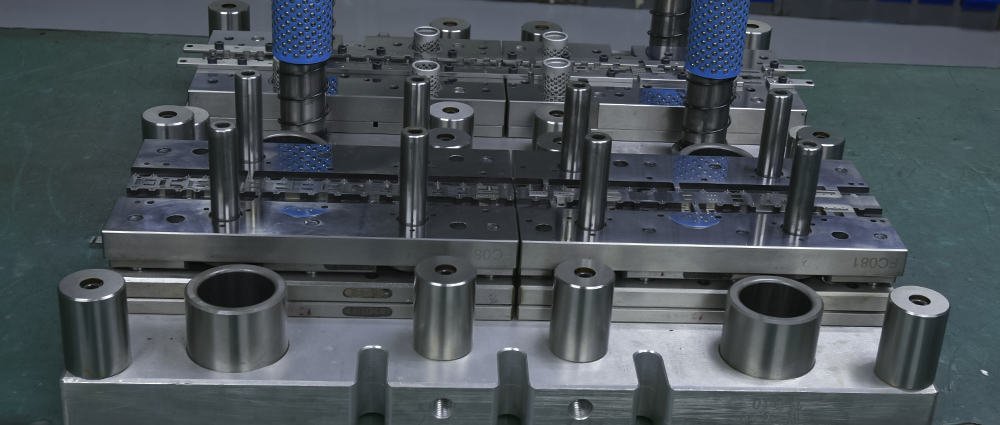