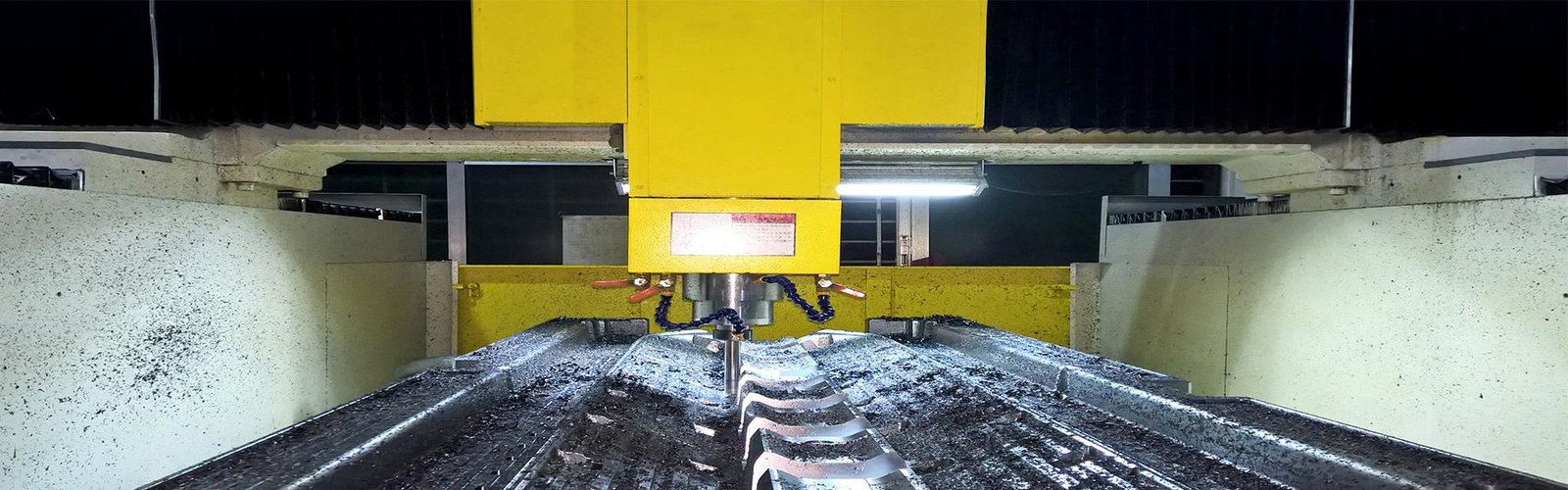
The World’s First 3D Printed Wind Turbine Blade Mold, More Than 10 Meters Long
In the public’s cognition, perhaps 3D printing can only do some gadgets. The tens of meters of wind power generator seems to have nothing to do with 3D printing. The Sandia National Laboratory once again refreshed our understanding. Sandia explored 3D printed solar panels last year, and recently developed the first wind-sinking giant blades made from 3D printing dies. This resulted in the 2018 National Technology Focus Award for the Technology Transfer Federal Laboratory Alliance.
Wind energy is one of the most promising resources for sustainability and reliability, but the wind turbine technology used is still not perfect. The average turbine blade size means that testing and prototyping can be too expensive and time consuming. Compared with traditional casting methods, 3D printing can solve this problem because of its improved design flexibility and production efficiency.
Using 3D printing technology can greatly shorten the prototyping phase of new turbine blades. Traditional methods for making molds are time consuming and labor intensive, and each new model prototype will take about 16 months to complete, and the blades can eventually be built and tested on it. The application of 3D printing molds has reduced the time to just three months.
In addition, Sandia also won the FLC’s Outstanding Technology Transfer Award for advanced nanomaterial window films, saving consumers billions of dollars in energy costs each year.