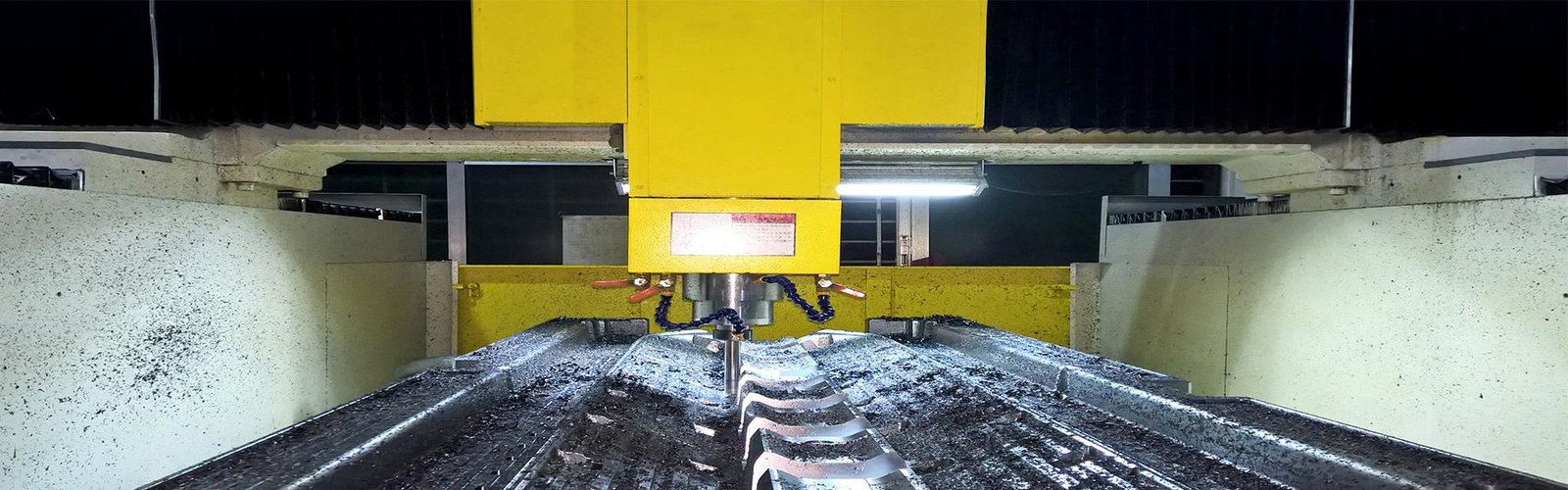
Extrusion Process Leader
Davis-Standards has always sought to enhance the performance of the extrusion process. Its new direct-drive Helibar® tank feed extruder has a grooved feed zone and a spiral grooved barrel. New barrier hybrid feed screw technology. The combination of the extruder and the feed screw provides a higher processing process flexibility due to higher recyclate utilization and pressure stability. It also handles a wider range of polymers at lower internal pressures and improves energy efficiency. The advantages of the Helibar® design are higher throughput, higher solution pressure, lower solution temperature, and better Solution uniformity, lower barrel wear and shorter residence time. It can be applied to pipes, profiles, sheets and blow molding processes.
Davis’ soft pack technology is designed to increase productivity and reduce resource waste in a wide range of applications. Davis-Standard was originally targeted at blown film, extrusion coating and liquid coating markets for soft and hard packaging applications. , as well as the industrial and construction markets. Innovative examples of waste reduction include cutting with high-precision articulation to reduce waste of material at the end of the product to a few inches, and providing effective cutting with a clean-cut and wrinkle-free fixed cutter winder Winding start-up action Recently, Davis-Standard sold a thermoplastic polyurethane and thermoplastic laminate for high transparency, and an aseptic packaging line with a production speed of 800mpm. All soft pack solutions are dedicated to increasing line speeds, faster conversions and significantly reduced product waste.