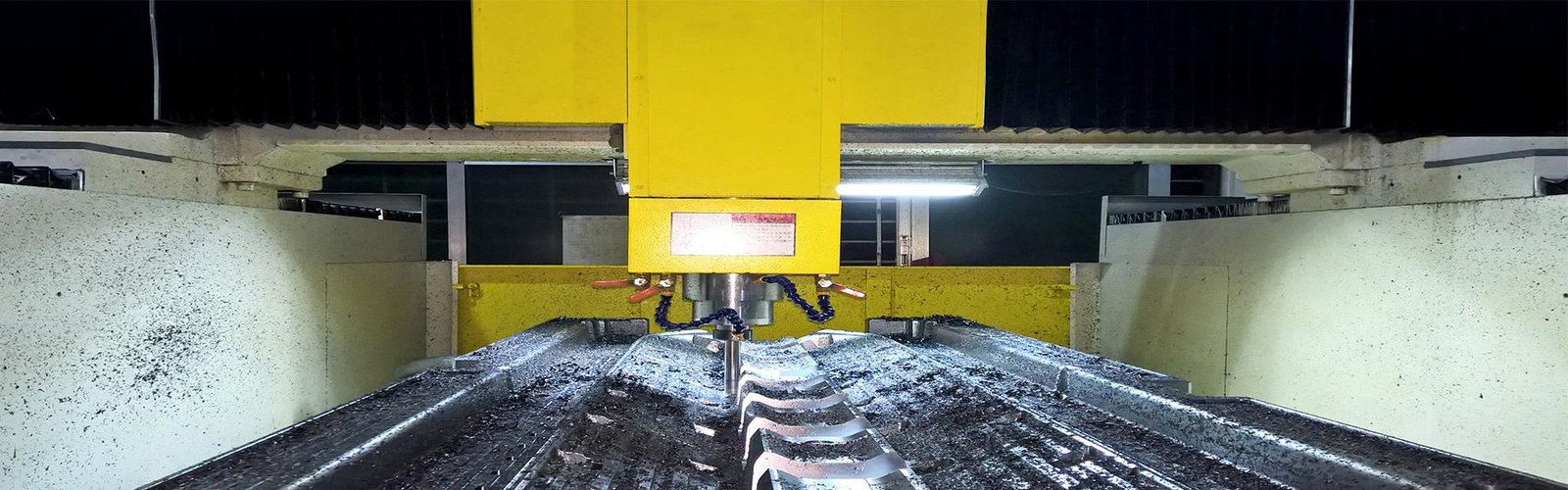
PPS Can Be Used For Forced Demolding Of Automotive Engine Cooling Systems
Engineering plastics supplier Polyplastics Co., Ltd. has recently completed an extensive study demonstrating that polyphenylene sulfide (PPS) can be used for forced demolding of automotive engine cooling systems.
Polyplastic’s linear DURAFIDE(R) PPS offers outstanding performance compared to similar products such as Nylon 66, and currently has a forced release function without deburring.
Forced demolding removes burrs that “bump” from both directions and can be ejected from the mold without the use of a sliding construction. The parting line (mould lip) disappears and a burr-free mold is realized. Prior to this, PPS was of limited use in forced demolding of engineering parts due to its fragility.
Polyplastics found that materials with high flexural fracture toughness in high temperature environments (150 degrees Celsius for PPS) are ideal for forced demolding in terms of damage and deformation. The company also found that it is possible to improve fracture toughness in high temperature environments by reducing fillers, increasing elastomers, and utilizing high molecular weight PPS.
Polyplastics has confirmed that the linear PPS has better fracture toughness than crosslinked PPS, which is more conducive to forced demolding. From the perspective of toughness in high temperature environments, Polyplastics’ DURAFIDE PPS seems to be suitable for forced demolding. Among the DURAFIDE PPS materials, high molecular weights 1130A1 (GF30%) and 1140A1 (GF40%) appear to be useful for forced demolding.
Polyplastics believes that DURAFIDE PPS can improve product reliability, and forced demolding reduces the deburring process and helps to increase design freedom. DURAFIDE PPS is also extremely resistant to high temperatures and is resistant to temperatures from 200 to 240 degrees Celsius. It also has better chemical resistance than fluoropolymers and has higher steric stability and lower hydrolysis rate and water absorption than nylon 66.