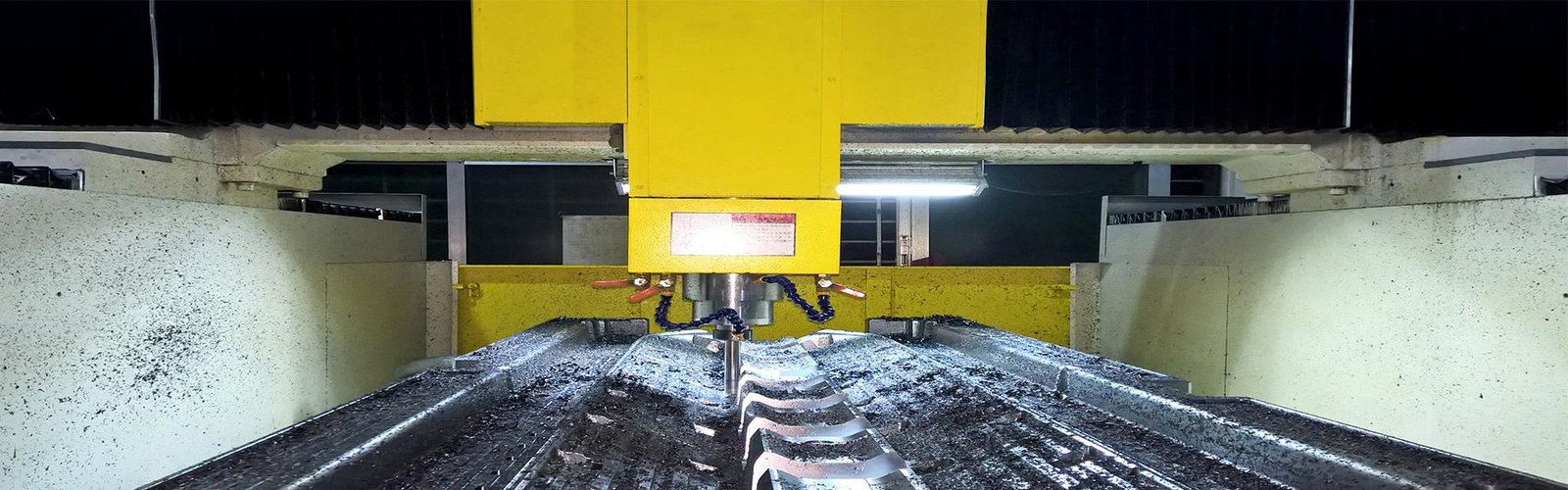
Advantages Of The IMT Process For The Injection Molding Industry
The IMT process uses a two-layer optical texture diaphragm that produces a three-dimensional optical 3D effect.
In the production of 3D curved mobile phone back cover, there is no significant difference in the appearance of the product between the IMT injection molding process and the composite sheet. The material cost and structural cost are mainly between the two.
The first is the cost of materials. When manufacturing the 3D curved mobile phone back cover, the IMT injection molding process can be completed in one shot, while the composite sheet needs to be printed on the whole PVD and texture, and then subjected to hot bending, hardening, CNC and other processes, in order to achieve the same. effect. In the post-manufacturing process of composite sheet metal, there is a problem of safety margin, which leads to waste of materials, and the overall material cost is inevitably higher than the IMT process.
Second is the overall structural cost of the mobile phone. The 3D curved mobile phone back cover, like the glass, is a pure decorative part in the product structure of the mobile phone. The overall structural load of the mobile phone is pressed on the middle frame, which will result in higher selection of the middle frame and more structure. complex. The cost of the middle frame is inextricably linked to its structure: for each hole in the structure, there is one more process, and the cost increases.
IMT injection molding can be used as an integrated back cover with edging and assembly structure such as buckles, which reduces the complexity of the metal middle frame, thereby greatly reducing the cost of the overall structural components of the mobile phone.
IMT brings together the advantages of various decorative processes, adopts the advantages of IML process in diaphragm manufacturing, absorbs the advantages of IMR process injection molding into in-mold transfer, combines digital printing and offset printing effects with traditional screen printing process to make IMT The process has strong applicability and wide application, which makes up for the limitations of the traditional appearance decoration process and meets the high-level innovation requirements of the product appearance decoration. The IMT process achieves 3D stereoscopic effects and product stretching, meeting the needs of more in-mold decorative processes. At present, Japan and Germany’s IMT technology is temporarily leading.
In summary, the IMT process not only greatly reduces the components of the mobile phone, making it resistant to corrosion and scratches, but also has a more attractive appearance. This requires plastic materials for IMT processing to have good low-temperature moldability (flowability), excellent chemical and impact resistance, excellent adhesion and high flame retardancy. The medium-plastic high-performance PC 5010-IMT series materials are excellent enough to meet the requirements of this process.