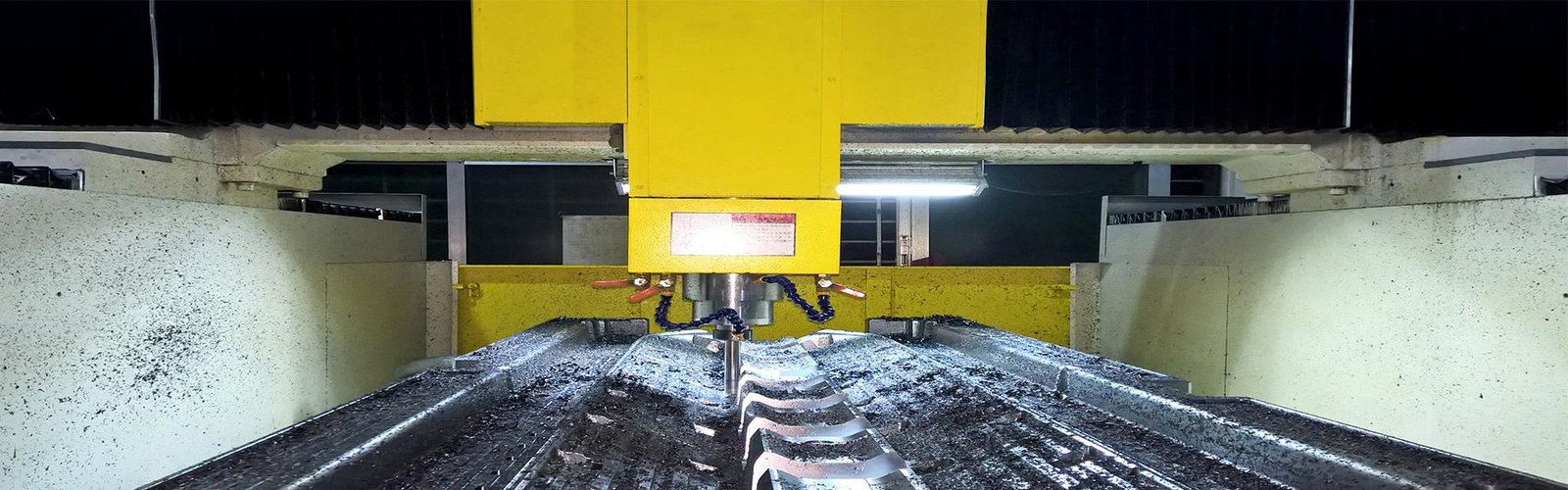
Self-Cleaning Pulverizer For Blow Molding Process
As the market continues to evolve and technology continues to advance, the materials and colors in the blow molding process change more and more frequently. Considering that it takes an average of 20 minutes to clean a standard machine, the cleaning steps must be completed as quickly as possible and reduce human intervention.
In this regard, TRIA, a manufacturer of Italian cutter crushers, conveyor systems and crushing systems, has developed a high-tech solution that introduces four crushers in the 40 and 42 series that can be fully assembled into the blow molding machine. It can also be installed as an independent shredder.
The company said several devices in standard machine configurations have contributed to achieving the goal. The compressed air nozzle is placed in the pulverization chamber and the hopper, and the active ionization rod integrated in the hopper removes the electrostatic charge in the recycled material and dust.
In addition, the air nozzle, shredder motor, suction system and funnel oriented air vibrator are driven by a simple PLC controlled automatic Stop&Go cycle unit. These device operators can remove and separate the pulverized material and dust from all internal parts of the pulverizer in just 5 minutes, so that it can be easily cleaned by suction.
TRIA noted that several long-term tests conducted at customer sites and original equipment manufacturers demonstrate the advantages of this solution. Compared to standard machines, the amount of residual comminuted material and dust is reduced by approximately 80%, and the final manual cleaning time is reduced by 60-80%, depending on the machine’s specifications. Usually the most difficult to clean hopper and crushing chamber can be self-cleaning, with only a small amount of comminuted material remaining on the screen and funnel.